It’s not surprising that more and more industries are turning to wireless technologies where risk management is important in order to monitor their operations. To properly and safely monitor long term projects that could last a decade in the mining sector, the use of IoT wireless monitoring can play a huge role.
By digitizing mining operations because of increased competition in the global mining and metals market, this has forced mine operators to rethink their operational strategies and increase safety and accuracy in their mines.
Changing how material is transported, reducing staff exposure to on-site hazards, minimizing damage to mining equipment, and optimizing production are some of the strategies used by mine owners to increase profitability. Autonomous mining equipment and vehicles, such as trucks, controlled by operators in the control room, are being used to transport material from underground tunnels up to the ground level. The first step to realizing the benefits of autonomous mining equipment is to embrace technologies that can facilitate their smooth movement and control.
SpiderMesh in Underground Mining Environment
Having specialized in challenging radio frequency environments, we wanted to test our technology and equipment in order to be fully prepared for future mining projects. Therefore, in order to assure that SpiderMesh technology performs well in a mining environment, we decided to run important tests in a mining site.
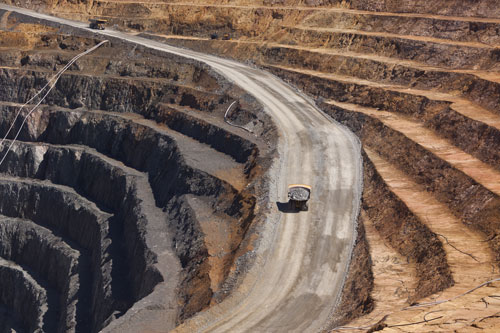
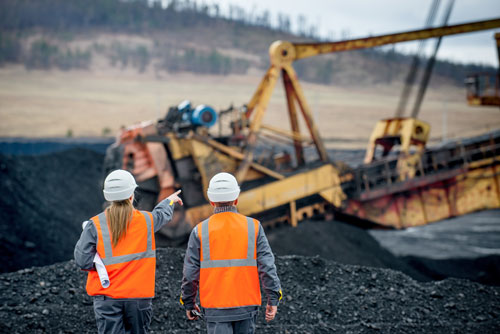
There are a number of factors that were taken into consideration when conducting our tests.
Range with high obstruction (90 angle turn)
Range with low occlusion (Straight drift)
Range with high and low data rates (50 kbit/s and 6.25 kbit/s)
Reliability
Main issues we wanted to tackle: Working Around Communication Barriers in Underground Mines
One of the issues that you can encounter when setting up the transmission of data is the structure of the mine itself. The process of implementing new processes and deploying equipment requires a fundamental shift in mindset for mine owners. If you’re using wires for your connectivity in the mine, there could be some constraints while connecting equipment to your control center. You could also face interference because the hazardous mining environments often disrupt communication with the control center, resulting in reduced operational efficiency.
Another key challenge is ensuring that networking devices are rugged enough to be deployed in underground mines to ensure continuous production.
Wireless Technology that can tackle underground mining connectivity challenges
So, how can wireless technology help the mining industry overcome the communication barriers due to harsh conditions in underground mining tunnels? Using sensors to detect movement, gases, or structure pressure is a crucial aspect in order to maintain worker safety. The setup cost and maintenance of wireless technology is also another added benefit of wireless technology.
On Location: Characteristics of the site
The tests were conducted at Cité de l’Or in Val d’Or, an old gold mining structure that is now converted to a museum and into a test site.
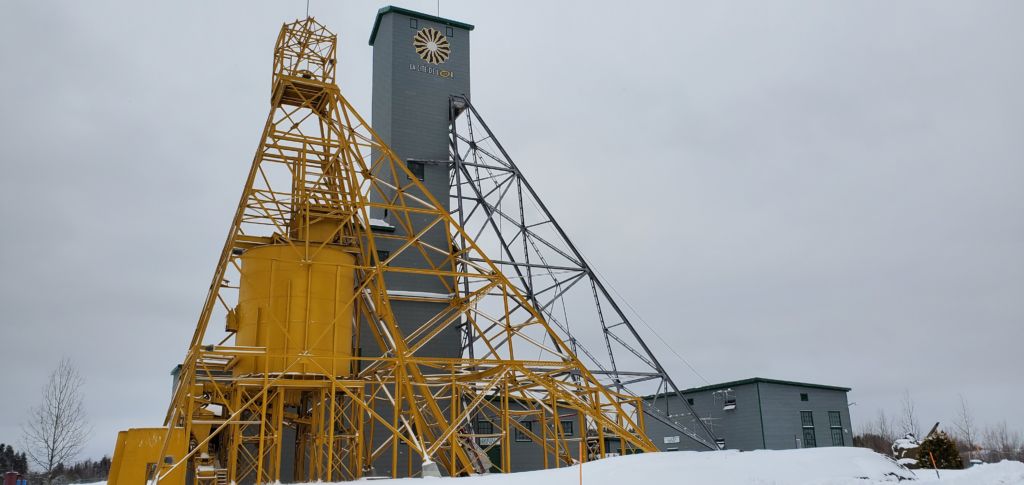
Here are a couple of interesting facts about this particular gold mine.
- Only site in Canada where visitors can explore a gold mine
- Visitors can witness the beginning of the 1920 gold rush in Quebec
- An underground visit at 300 feet (91 m.) of a real mine drift
The area is 600m total length and is 91m in depth underground. The drift size (or tunnel size) is 2m in diameter.
Test 1
Objective:
The first test that was conducted was to verify the wireless performance of the Portia radio module. Specifically, we wanted to measure the exact range between two nodes underground, in a typical mining drift environment.
The objective was also to determine the optimal data rate that can be used in these conditions. As we know, wireless performance leads to compromises and therefore, node-to-node range can be increased with a network speed tradeoff.
Process:
A gateway was installed on the ceiling of the drift at the garage section.
Then a range test was performed on the downward section with a 90-degree sharp turn in order to test for a worst-case scenario. To achieve this, we moved a connected node further down the elbow until synchronization with the gateway was lost. We then measured the resulting distance traveled.
Results:
We specifically conducted these tests in the most severe conditions with an approximate drift diameter of 2m. Of course, if we were to increase the size of the tunnels that are more accurate to current mines (4.5 to 5.5 m), then we can expect a reasonable increase in range.
Our first test was done with Portia configured at 50kbit/s. The resulting range in this challenging setup was 400ft. Then, we evaluated the increase in range when lowering the data rate. With 6.25kbit/s, we were able to walk down another 300ft. Both the gateway and the node had an omnidirectional 3db (dbi, dbm db) duck antenna.
Test 2
Objective:
The objective of our second trial was to determine communication reliability and stability with a full mesh deployment. A node was placed every 200ft (i.e at least 2 nodes per hop) during this test. We also wanted to know how many hops were needed in order to relay a reliable signal to the end of the tunnels. With this information, we wanted to confirm whether it’s possible to cover an entire mine on a single gateway.
Process:
We’ve deployed 13 nodes over the full 600m tunnels. 8 nodes were placed in the main drift on the sidewalls and the others were scattered in two adjacent tunnels. A node was placed every 200ft. Once the network was deployed, we first checked the hop position of each node. This information is stored in each Portia module. Therefore, we carefully examined each node individually and requested for their hop status.
The Results:
The results were promising. Only 4 hops were required to cover the main drift. Two additional hops were used to connect adjacent tunnels. Moreover, hops 1 and 2 had multiple redundancies (many nodes on the same hop level). This indicates that it might be possible to trim down the network a little bit and optimize node placement.
Next, we wanted to evaluate how reliable our mesh network is in this deployment. We set the gateway at 20% duty cycle, and 8 hops. This means that the gateway polls a node once every 800 ms. At this rate, we receive new data every 9.6 s. Of course, it’s possible to poll the network faster by implementing parallel polling or by changing either the data rate of the network or even the packet size.
For the purpose of this test, the network was configured at 50kbit/s and 20 bytes packet size.
Process:
We polled the sensors 784 times and found out that communication was 100% reliable as we did not have any packet loss.
Since the mesh was performing very well, we decided to remove two redundant nodes in the relatively straight portion of the drifts. With the devices removed, there is a 600ft ‘’jump’’ between two adjacent nodes. Although there were no sharp turns in that drift section, there were still elevation differences (bumps and dips). Therefore, there was no real line-of-sight.
Once the nodes were removed, we once again verified the mesh topology and analyzed the hop status of each node.
The results for the number of hops required were similar as before, with the mesh surprisingly performing a little bit better. This is because there is always a small variation every time we check for the hop status of the nodes. A node can be at the limit between two hops and can switch from one to the other at anytime.
As for the reliability, we polled the nodes 1258 times and once again, we had a 100% success rate with no packet loss.
In conclusion, mesh behavior was as expected and similar to deployments in a forested environment. Furthermore, it is definitely possible to deploy a SpiderMesh network that would cover an entire underground mine. Since the drift conditions would differ from mine to mine, we can expect variations in the range between sensors. However, generally speaking, modern mines have larger drifts to include large mining vehicles and therefore, the mesh is expected to perform better. Overall, the majority of mines should be able to connect seamlessly to a single coordinator. For larger mining facilities, it would be possible to reduce the number of hops required by sending the signal down from the gateway to the bottom of the mine through the shaft.
These are very promising results given that environments such as underground tunnels require a wireless technology that must extend well and also take sharp turns. For this reason, GHz technologies (802.15.4, 2.4GHz, 5.8 GHz, Bluetooth LE) do not perform well in such environments because they use high-frequency radio waves that cannot penetrate through walls.
Additionally, SpiderMesh operates on the sub-Ghz band, which is a lot less cluttered in mining environments. The noise floor is lower than other technologies and the remaining possible interference is not of concern since SpiderMesh uses a frequency hopping spread spectrum channel access scheme.
Our recommendation for future deployments
As a general rule, a node should be placed every 200 ft, or at each corner when there is a sharp turn. Afterward, the network should be monitored for a period of one week to test for reliability without a packet loss. Subsequently, we can trim down the network and remove at certain locations provided that we keep at least 2 nodes in the same ‘’hop’’.
Since the network will be divided into a long line of nodes, we must be careful not to have a bottleneck (only one node in a hop). Without enough redundancy, a node failure can take down the whole system. As in forest deployments, the network will be extremely reliable if we follow these instructions.
Additional notes
Instead of trimming down the network, we can also increase network bandwidth to 100k, gaining speed. If for some reason there are some environmental changes that result in decreased reliability, then we can always decrease the network bandwidth to 25k, 12.5k or 6.25k to increase the range of the nodes.
Extensometer
In mining, there is a device that is used in order to measure rock movement, this is an extensometer. It’s a cable with sensors that measure any kind of rock movement happening in the mines. This allows the monitoring of weak points in the structure throughout the years.
This tool allows you to detect faults and joints. Faults are when two types of rock meet in the ground and a joint is a fracture in the rock. These measurements are normally taken once a month by someone who manually checks and takes note of the results by hand.
This device is a crucial tool in the mining industry because it assures safety for the mine workers. This data that is captured from the extensometer can provide an early warning of displacement that could lead to a collapse. Additionally, the data gathered can be used to help prevent production disruptions, as potential problems can be reported and addressed before they become more serious.
Flowmeters
In order to measure any kind of liquids in the mine, flowmeters are used. They will be used to measure slurry flows and heavy media flows.
Fan Control
Ventilation is an important aspect when it comes to all mines, some fans are controlled from a control system up above, whereas others have to be manually activated by the workers. The downside to using the mine workers to manually control the fans is the risk of human error. Forgetting to turn them on can be dangerous and costly. There is also a risk of the site being blocked off for 2-3 hours until the gas levels are back to normal, which ultimately causes delays and comes with added costs, and hinders productivity.
Monitoring Water Levels
In mines, there is a lot of water that is used to cool drilling pipes and to clean holes and equipment. This water then falls on the ground and flows to the basin that was put in place for this reason. If the basin overflows, the entire level can be flooded and the section is blocked, since vehicles and workers cannot move properly. Therefore, in order to continue working, the entire section will have to be pumped. There are two typical situations that could cause an overflow of water. Either the pump stops working or the bottom of the basin is not cleaned properly and the particles accumulate block the pump.
SpiderMesh, Bluetooth, and Fiber Optic Cables
Bluetooth works well in short distances, less than about 10m or 30ft, but can become problematic if the devices fall out of range or if there are any sharp turns or uneven areas that could interfere with the frequency. It also consumes a lot of energy, which means it cannot be battery operated for a very long time. It would need to be recharged more frequently, as opposed to using SpiderMesh, which runs on low power (and a long range).
If there aren’t any fiber optic cables installed in the mine already, our technology works without it, unlike other technologies such as Zigbee, for example. Therefore, it’s an easy set up without any infrastructure cost.
SpiderMesh was designed for these more challenging environments such as mines. The technology is reliable, scalable, and cost effective. As we have seen throughout our tests, a node is needed only every 200ft, or 600ft, if it’s a relatively straight drift.
Complimentary
While Spidermesh cannot carry high bandwidth that controls remote vehicles, our technology is complementary to fiber optics. What is great about Spidermesh is when there are no fiber optics installed on site, the technology works nonetheless.
If there are plans to eventually install a fiber optics network, Spidermesh can also be set up as a temporary network because it can easily connect sensors back to the fiber optics network.
Using Spidermesh wireless technology is also a lot more cost-efficient, and can be easily set up for long term or short term projects. If the fiber optics network cannot reach a certain area in the mine, Spidermesh can be used as a sub mesh network, connecting the data back to the fiber optic cable.
Out technology is scalable, can cater to almost any environment, works well as a stand alone product or meshes well with existing technology as well.